How to Pick the Right Warehouse Layout to Improve Operations
Table Of Content

This is one of the best-kept secrets of warehouse layout optimization, especially in the West, where we’re typically blessed with much larger spaces. An optimized warehouse also allows for better visibility of workers throughout the facility. That way, supervisors can quickly intervene if needed and help ensure that employees are adhering to safety guidelines.
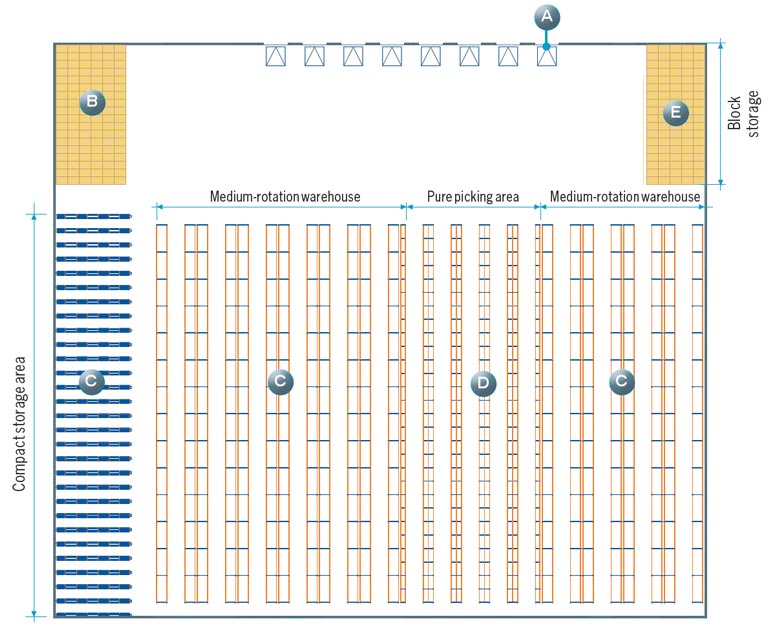
Step 2: Space Evaluation
These goals, such as improving order fulfilment or cutting down on shipping and delivery times, will aid in the design planning process and provide direction for your warehouse layout. If you have enough square footage, create separate packing zones for items that will be delivered versus items that will be shipped using third-party couriers. Products need to be packaged, weighed, and labeled differently, depending on which delivery or shipping method you’re using. So the more you can separate these two systems, the better.It may also help to designate different loading docks for different couriers.
Step 8: Safety Prioritization
Begin by categorizing products based on similarities such as size, shape, weight, and storage requirements. Grouping similar products together streamlines the warehousing process by creating dedicated zones for specific types of inventory. Consider the vertical dimension of the warehouse by evaluating the building height.
Costco store layouts change constantly — employees have some tips - Business Insider
Costco store layouts change constantly — employees have some tips.
Posted: Sun, 29 Apr 2018 07:00:00 GMT [source]
The Holistic Impact of Safety Prioritization
The goal is to create a streamlined flow that minimizes unnecessary travel and handling times. Efficient space utilization is a natural byproduct of a well-executed inventory assessment. By categorizing products based on size and weight, you can allocate storage space more effectively, ensuring that every square foot of the warehouse contributes to overall productivity.
Continuous monitoring of system performance, regular software updates, and the incorporation of new features are essential. This proactive approach ensures that the warehouse stays ahead of the curve in technological advancements. The ideal solution is for the management office to be located in the reception and dispatch area and, if possible, between these two areas.
The right layout should help to improve the flow of production and distribution. Creating the warehouse space of your dreams is all about optimizing what you have, what you need, and what you want. With a warehouse layout, your organization can customize warehouse movement and increase overall inventory accessibility.
Consider Operational Efficiency
Depending on existing warehouse floor space, some layouts may be more expensive to create and sustain than others. Finding a suitable layout means becoming very aware of what materials are available and where staff will fall into place. Running a successful warehouse requires careful planning and an organized system. In this blog post, we discussed many tips to help you improve your warehouse layout and improve your overall profitability. Moreover, RFID systems can be used to track products from the moment they enter the warehouse until they are shipped out. This helps ensure that all items are accounted for at every step of their journey.
You may create a layout for your warehouse that will guarantee an adequate flow of goods and allow room for the appropriate equipment by gathering and analysing this data. When designing the layout of your warehouse, it is crucial to ensure the continual movement of supplies, workers, and equipment. You can prevent inefficient paths and disruptions by properly arranging your warehouse layout design to enable each function sequentially.
The Significance of Workflow Efficiency Design
Smart Warehousing: What It Is and How It Can Help Your Business - Thomas Insights
Smart Warehousing: What It Is and How It Can Help Your Business.
Posted: Mon, 13 Nov 2023 08:00:00 GMT [source]
In the realm of bulk storage, pallet shuttles shine as architects of efficiency. Their automated movements within racking systems facilitate high-density storage of palletized goods, minimizing the need for extensive manual handling. This advanced automation not only enhances efficiency but also reduces the risk of errors in large-scale storage operations. These systems should have the flexibility to accommodate changes in product flow, picking sequences, and packing processes.
Optimizing warehouse picking processes and/or implementing order picking software are two of the most effective ways to optimize the supply chain. Depending on the warehouse size, number and types of products in it, and total staff count, one picking strategy may suit you better than others. Warehouse best practices include choosing the right inventory storage system that will optimize the picking, packing, and shipping process to ensures order accuracy, efficiency, and speed.
Shaped like a semi-circle, the U-shaped design idea usually has the loading and shipping areas next to each other. The reception area is usually behind the loading and picking area (behind shipping). Plus, their easy-access design makes them an efficient alternative to stocking small goods in closed boxes, and they can be easily color-coded. Take note, though, that if you want to maximize the height of your warehouse for extra storage space, you won’t be able to do that with LD shelving, as these units are usually only 6’ to 7’ high. If your warehouse plans involve hand-stocking small boxes for assembly or pack-and-ship, hand-held bins or rolling carts are all you need to stock and pull stored goods. In these cases, your shelving aisles will likely need to range between 3.6’ to 4’ wide.
This data-driven approach allows for proactive decision-making and adjustments to further optimize the workflow. Maximizing vertical space aligns with principles of environmental sustainability. By making the most of existing warehouse space, businesses can minimize the need for land expansion, contributing to reduced environmental impact and resource consumption. The primary advantage of vertical space utilization is the enhanced storage density it offers. By stacking goods vertically, warehouses can accommodate a larger volume of inventory within the same physical footprint, optimizing every cubic meter of space.
Guaranteeing the happiness of those who keep your warehouse running is essential. Employees are happy when they know exactly what is expected of them and how they can succeed in their roles. When implementing a new warehouse layout, a training process must be developed so all warehouse staff understands the flow and what they need to do to ensure smooth movement throughout the floor plan. After creating a blueprint of the warehouse and collecting measurements, you can start planning how different warehouse components can be set up.
Operational processes within a warehouse are subject to refinement and innovation. Flexibility for Future Changes necessitates a layout that can seamlessly integrate modifications to operational workflows without disrupting the overall efficiency. Incorporate scalable storage solutions that can be easily adjusted to accommodate varying inventory sizes. This includes adjustable pallet racking systems, modular shelving units, and dynamic storage configurations that can expand or contract based on the volume of goods.
This includes offices, employee spaces, dynamic storage, static storage, staging areas, and shipping and receiving docks. All major areas should be accounted for, including assembly lines, manufacturing materials, work benches, conveyor belts, and other equipment that require allocated space. The I-shape warehouse design has a straight flow from receiving to shipping and vice versa.
Comments
Post a Comment